Costing Techniques: Full Costing vs. Contribution Costing (31.3)
- Thiago Casarin Lucenti
- Feb 17
- 4 min read
Chapter 32 - Costs
Lesson Objective: To understand the difference between full-costing and contribution costing
Let's get started with the two costing techniques we are up to discuss by looking at:
1. Full Costing Technique (Absorption Costing): a technique in which all fixed and variable costs are allocated to products, services, or divisions of the business
On this technique the total overheads is divided between each product and cost centers on the proportion of total direct costs of each of them;
It could also be that overheads are divided on the basis of factory/office space taken up by each product or service.
In summary:

Example 1 (Simplest):
A pump manufacturer produces 5 000 pumps per year.
Total direct costs = $100 000
Total overhead costs = $50 000
Full cost of producing pumps = $150 000
Average (or unit) full cost per pump = $30
The problem happens when the business produces two or more products. How will the allocation of indirect costs be?
Example 2: Allocating indirect costs evenly across products:

Inaccurate as it attributes indirect costs equally among products with very different direct costs as well as far apart in annual output.
- It will lead to wrong price decisions and make product B may become uncompetitive.
The solution?
Example 3: Attributing indirect costs proportionally to direct costs or output:

More accurate full cost figures are obtained, which will be much more useful for decision-making such as setting prices.
The advantages of this technique are clear:
Easy to understand and calculate;
Best used for single-product businesses (no doubts about cost allocation) for pricing decisions - cost-plus pricing technique;
No costs are ignored (all costs are allocated, always);
It is used for comparisons to assess performance overtime.
Its limitations, however, are:
The allocation of costs might be unfair (e.g. a product that takes up a large factory space but use low-cost and easy to maintain machinery will have more overheads allocated to it) - Example 3;
Can mislead decisions since the results it generates can be wrong if the wrong allocation method is picked up (proportion of factory space used, proportion of total labor costs, proportion of the output, etc.);
Can lead to inconsistencies when different methods of allocation are used - it is advised to pick and continue with the same allocation method.
Activity 31.3 #1 (a, b, c)
2. Contribution Costing (a.k.a. Marginal Costing) a technique that allocates only direct costs and does not consider overhead costs.
It focuses on the marginal cost (the cost of producing one extra unit), which is a variable direct cost.
Example:
The total costs of producing 100 units of a book is $400,000;
The total costs of producing 101 units of a book is $400,050;
The marginal cost (extra cost for one unit) is $50.
Therefore, the contribution of a product is the revenue from selling that product minus its marginal cost (variable direct cost).
Contribution is different than profit: to calculate profit overheads need to be considered!
If that 101st book (marginal cost of $50) is sold for $70, it has made a contribution towards the fixed costs of $20.
Example:
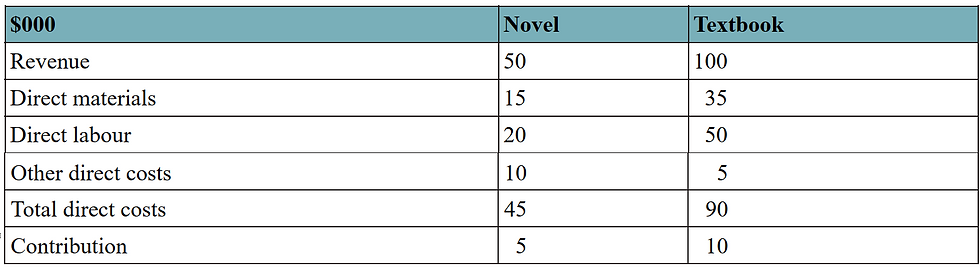
To calculate profit, in this case, you would need to subtract the total indirect costs ($12,000) from the total contribution of both products ($15,000) which = $3,000.
Activity 31.4
Contribution Costing and Decision Making:
Contribution Costing is better than full-costing for making decisions as it does not allocate overhead costs between products:
- It shows which products (among all) are making the greatest and the least contribution towards covering overheads and towards profits.
- Full costing could lead a manager to stop making a product because it seems like it is loss-making even though the product is making a positive contribution towards indirect costs.
Contribution Costing helps to decide on whether to stop making a product or not:
It shows which products are making more or less contribution to covering for overheads and profits;
The application of Full-Costing may seem like a product is loss-making but it hides the fact that it might be making a positive contribution to the overall profitability - stopping the production of such product will reduce the overall profit of the business since the fixed overhead cost will still have to be paid but now with reduced contribution to pay them off.
Activity 31.6
Contribution Costing also aids on deciding whether the business should accept selling its products/services at a lower price than its full-cost of producing it.
As for example in case of spare capacity (e.g. off-peak season for hotels) or simply because it’s trying to enter a new market.
Selling a product at a lower price than its full-cost may increase overall business profitability as there will be more contribution towards overhead costs and fixed costs:
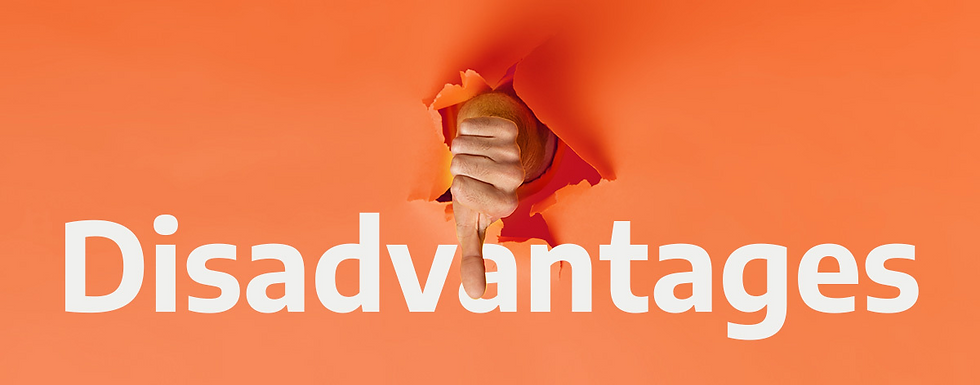
May hurt the brand image;
Brand may be seen as a lower-priced one;
It can be hard to increase prices again;
Other people/businesses may buy at lower price and resell later for higher prices.
Summarizing the two different costing techniques - when is one better than the other?
Full-Costing is more useful for single-product firms as it offers a quick guideline to the costs of a product. It presents several flaws when it comes to multiple-products companies due to how it distributes overhead costs among the various products.
Full-Costing can also bring about inaccurate figures which can be useful for comparisons when the same allocation method is used but is not used for decision-making;
Full-Costing is used for expansion decisions as it considers all possible costs;
Contribution Costing on the other hand is useful for pricing decision-making but on the other hand ignores overhead costs - although it realizes their existence;
Contribution costing can be used in decision-making over whether to close a cost/profit center depending on their positive/negative contribution;
Special orders decisions: excess capacity is more likely to be effectively used, if special orders or contracts that make a positive contribution are accepted.
A big disadvantage of contribution costing is that it may lead managers to maintain the production of goods just because of a positive contribution when other better decisions could be made (e.g. introducing another product with an even greater contribution).
Remember: regardless of the quantitative results of the costing techniques businesses should also consider qualitative factors in their decisions (e.g. brand image).
To-Do-List:
Activity 31.7
Activity 31.8
Chapter 32 - Costs
Comments