Quality: Standards, Control, Assurance, and TQM (27.1)
- Thiago Casarin Lucenti
- Nov 17, 2024
- 4 min read
Chapter 27 - Quality Management
Learning Objectives: To understand quality control, assurance, and TQM.
In your opinion, what is a quality product?
The most reliable?
The best performing?
The longer lasting?
Quality is a relative concept which depends on variables such as:
Price;
Customers' expectations;
Customers' satisfaction.
A quality product, therefore, is one that meet customers’ expectations and therefore fit its purpose.
Can a highly priced good be of low quality?
Can a cheap good be considered high quality?
And that's why businesses implement so called Quality Standards, which are nothing but the expectations of customers expressed in terms of the minimum acceptable production or service standards. Such information is found through Market Research.

Quality Standards for goods and services is different:
For goods it's expressed as the reliability of the product (e.g. cars), its design (e.g. clothes), robustness, weight, battery life, etc.;
For services it's expressed differently: waiting time, kindness, knowledge, etc.
We know the many advantages from offering quality products and services:
Loyalty, repeated purchases, and long-term financial stability;
Cost saving from complaints, compensations, replacements;
Longer product life-cycles - savings on costs of development;
A quality image leads to reduced cost and need of advertisement;
Potential higher profitability due to the ability of charging premium.
There are mainly two approaches for achieving quality:

Control is based on inspection/checking of the completed unit;
Assurance is the process of self-checking quality by the workers in charge of each process preventing and reducing faulty products.
Control, therefore, can be problematic:
Workers and inspectors live in a conflictual situation leading to a bad corporate culture (motivation);
Inspecting is a tedious job and demotivation leads inspectors to underperform on their jobs;
A faulty product might go through many different stages of production before being spotted (costly, time wasting process);
QC takes away from workers the responsibility over quality.
There are different methods of Quality Control:
Prevention: 'Quality should be designed into a product.'
- The product design should satisfy the requirements of the customer and allow for accurate, error-free production;
Inspection: Involving high-cost, technically-competent inspectors to check the finished product:

Correction and Improvement: Also focus on fixing faulty products, but...
- It includes the correction of the process leading to faulty products to improve future quality.
Activity 27.3
Now that we are all convinced that Quality Assurance is a better process than Quality Control, let's look at the stages of Quality Assurance Methods:

1. Product Design: QA is involved in making sure that the product will meet the customers' expectations in the first place;
2. Quality of Inputs: Suppliers are held accountable for delivering components meeting the agreed quality standard;
3. Production Quality: In charge of not letting quality standards drop below pre-set standards by coordinating workers and accountability among employees;
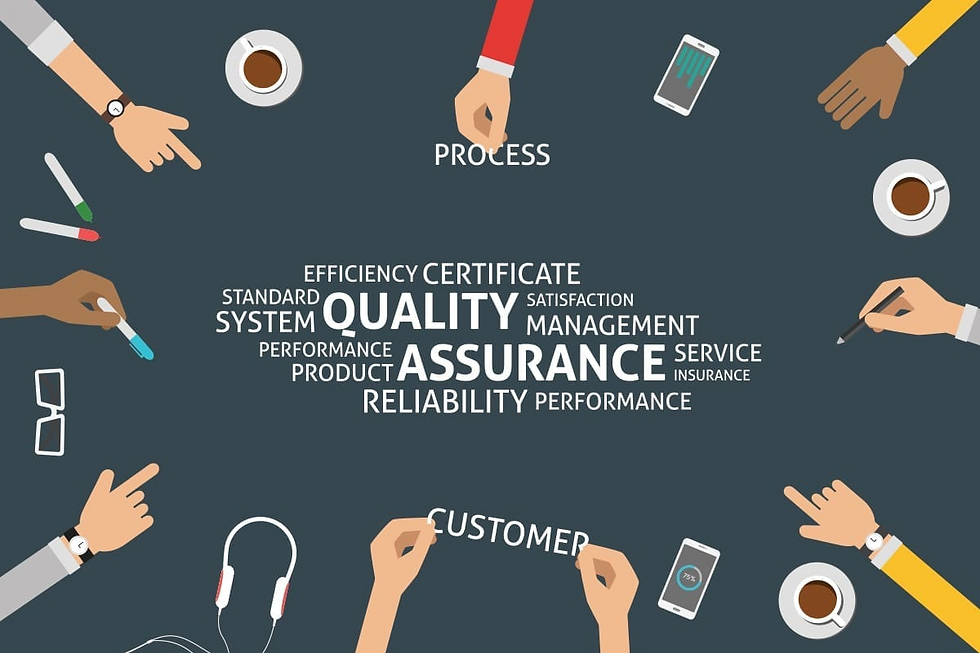
3. Delivery Systems: Monitoring punctuality and reliability of delivering products to customers is also looked into by QA;
4. Customer Service: Continued customer satisfaction depends on the quality of the contact with customers in post-purchase situations.
Implementing QA can bring other indirect advantages to businesses:
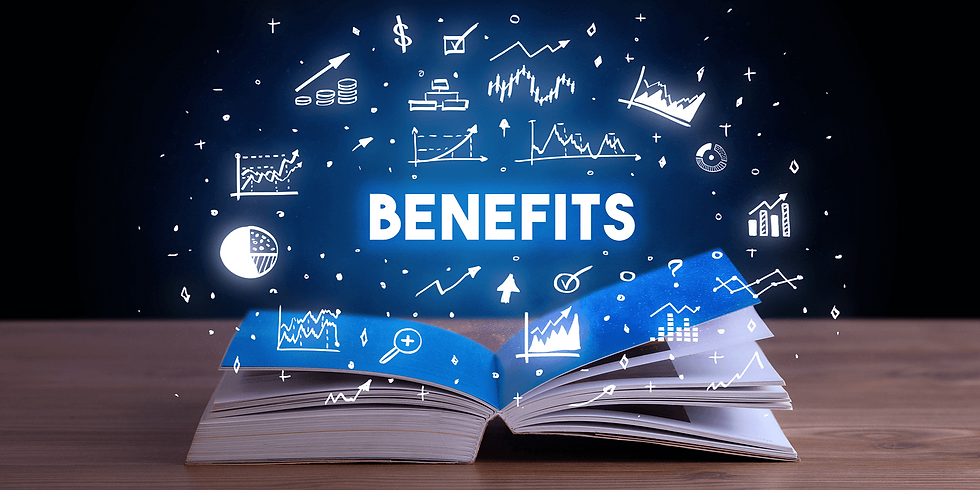
Workers' motivation - teamwork and involvement in the process;
Reduce final inspection costs;
Quality-related costs are reduced (waste, defects);
Possibility for quality accreditations leading to status (marketing opportunities):
The ISO 9000 is a good example - a certificate to acknowledge the existence of quality assurance within a firm. To be awarded the certificate requirements need to be met:
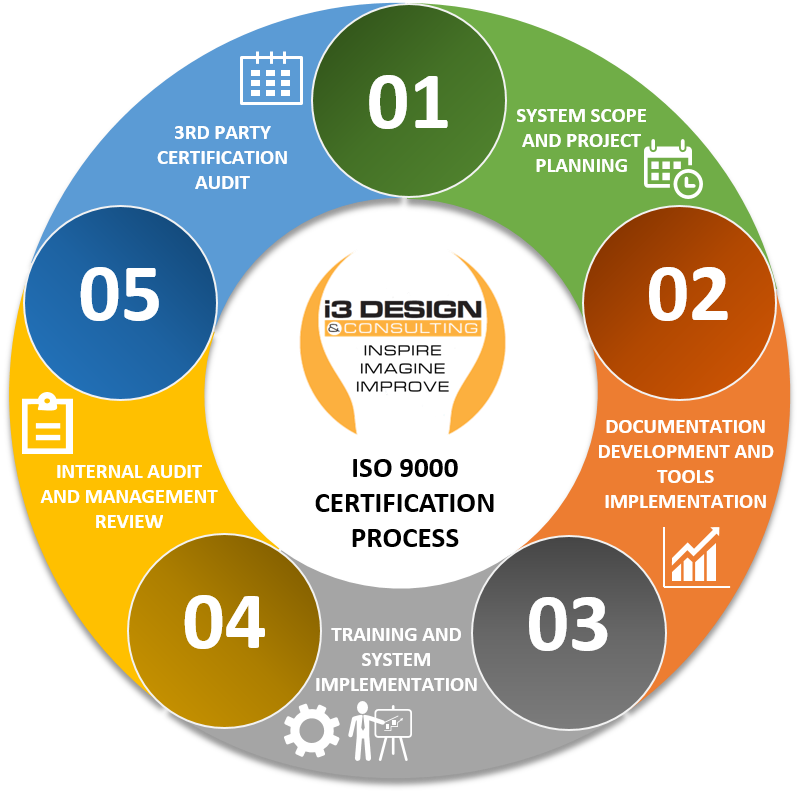
Implemented staff training and appraisal methods;
Implemented methods for checking the quality of inputs brought in by suppliers;
Implemented quality standards initiatives in all areas of the business;
Implemented standard procedures for dealing with defective products and quality failures;
Implemented standards for after-sales service.
On the other hand, such awards are costly to prepare for and very bureaucratic.

Finally, TQM is another important concept when it comes to quality:
TQM is not a technique – it is a philosophy that quality is everyone’s responsibility.

- TQM’s aim is to achieve zero defects always;
- The process puts the business as if having internal customers who will receive some work/product from someone else and therefore depends on the quality of that input;

To be effective, TQM requires:
A deep change in the company culture where quality becomes everyone’s responsibility and not just someone’s else;
Trainings;
Empowerment and responsibility to all workers (in all levels) to check quality before passing on the product/service to the next step.
Quality-chains: every department is obliged to meet quality standards of their internal customers - a series of suppliers and customers relationships.
TQM fits in well with the Herzberg principles of job enrichment - every worker being empowered with the responsibility of checking quality before passing on to the next stage.
TQM will bring businesses many advantages:
Eliminate the need of a separate quality control department (↓ cost);
Reduce or eliminate faulty/defective products (↓ cost);
May increase the demand for the business products/services overtime due to quality.
Chapter 27 - Quality Management
To-Do-List: Activity 27.4
Comentarios